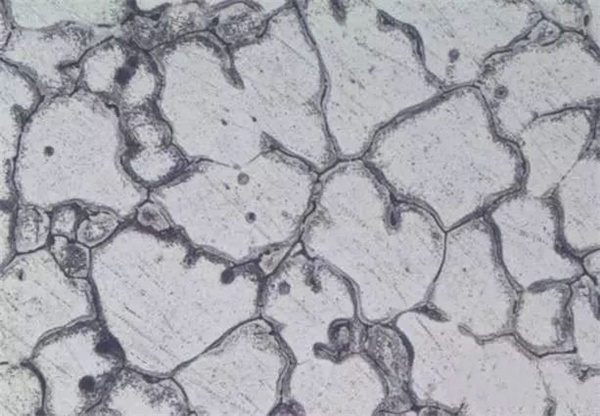
I. အတိုကောက်
ချဲ့ထွင်ထားသော ထုတ်ကုန်အချို့၏ အမြီးစွန်းတွင် ချဲ့ထွင်မှုနည်းသော စစ်ဆေးပြီးနောက်၊ အမြီးကျုံ့ခြင်းဟုခေါ်သော လက်ဝါးကပ်တိုင်အပိုင်း၏ အလယ်တွင် ဦးချိုကဲ့သို့ ဖြစ်စဉ်တစ်ခု ရှိသည်။
ယေဘူယျအားဖြင့်၊ ရှေ့သို့ထုတ်ထုတ်ခြင်းထုတ်ကုန်၏အမြီးသည် ပြောင်းပြန်ထုတ်ယူခြင်းထက် ပိုရှည်ပြီး ပျော့ပျောင်းသောသတ္တုစပ်သည် မာကြောသောသတ္တုစပ်ထက် ပိုရှည်သည်။ရှေ့သို့ extruded ထုတ်ကုန်၏ ကျုံ့သွားမှုသည် အများအားဖြင့် အဝိုင်းပုံ အဆက်အစပ်အလွှာပုံစံဖြင့်ဖြစ်ပြီး၊ ပြောင်းပြန် extruded ထုတ်ကုန်၏ ကျုံ့သွားမှုသည် အများအားဖြင့် အလယ်လမ်းကြောင်းတစ်ခု၏ ပုံသဏ္ဍာန်ဖြစ်သည်။
သတ္တုကို နောက်ကျောဘက်သို့ extruded လုပ်ပြီး၊ ဖောက်ထုတ်သည့်ဆလင်ဒါ၏အသေထောင့်တွင် စုပြုံနေသော အရေပြားနှင့် နိုင်ငံခြားပါဝင်ပစ္စည်းများ သို့မဟုတ် gasket သည် အလယ်တန်းကျုံ့သွားစေရန် ထုတ်ကုန်အတွင်းသို့ စီးဝင်သည်။ကျန်ရှိသောပစ္စည်းသည် တိုတောင်းလွန်းပြီး ထုတ်ကုန်၏အလယ်ဗဟိုကို မလုံလောက်သောအခါတွင်၊ အတိုကောက်အမျိုးအစားတစ်ခုဖြစ်သည်။အမြီးအဆုံးကနေ အရှေ့အထိ အမြီးက တဖြည်းဖြည်း ပေါ့ပါးလာပြီး လုံးဝပျောက်သွားတယ်။
ကျုံ့ခြင်း၏အဓိကအကြောင်းရင်း
1. ကျန်ရှိသောပစ္စည်းသည် တိုလွန်းသည် သို့မဟုတ် ထုတ်ကုန်၏ဖြတ်တောက်မှုအဆုံး၏အရှည်သည် စည်းမျဉ်းများနှင့်မကိုက်ညီပါ။
2. Extrusion pad သည် မသန့်ရှင်းဘဲ ဆီစွန်းထင်းနေခြင်း၊
3. ထုတ်ယူခြင်း၏နောက်ပိုင်းအဆင့်တွင်၊ ထုတ်ယူမှုအမြန်နှုန်းသည် မြန်လွန်းသည် သို့မဟုတ် ရုတ်တရက်တိုးလာသည်။
4. ပုံပျက်နေသော ညှစ်ပြားကို အသုံးပြုပါ (အလယ်တွင် မြှင့်ထားသော pad) ကို အသုံးပြုပါ။
5. extrusion ဆလင်ဒါ၏ အပူချိန်သည် မြင့်မားလွန်းသည်။
6. extrusion ဆလင်ဒါ နှင့် extrusion shaft သည် ညီညွတ်ခြင်းမရှိပါ။
7. သွားဖုံး၏မျက်နှာပြင်သည် မသန့်ရှင်းခြင်း၊ ဆီစွန်းထင်းမှုများရှိနေခြင်း၊ ခွဲခြားထားသောအကျိတ်များနှင့် ခေါက်ခြင်းနှင့် အခြားချို့ယွင်းချက်များကို မဖယ်ရှားပါ။
8. extrusion ဆလင်ဒါ၏ အတွင်းဘက်အင်္ကျီသည် သန့်ရှင်းမှု သို့မဟုတ် ပုံပျက်နေခြင်းမရှိသည့်အပြင် အတွင်းပိုင်းကို သန့်ရှင်းရေး pad ဖြင့် အချိန်မီ မသန့်စင်ပါ။
ကာကွယ်နည်း
1. အကြွင်းအကျန်များကို ချန်ထားပြီး လိုအပ်သလို အမြီးပိုင်းဖြတ်ပါ။
2. မှိုများကိုသန့်ရှင်းအောင်ထားပါ။
3. ingot ၏မျက်နှာပြင်အရည်အသွေးကိုတိုးတက်စေသည်;
4. ချောမွေ့စွာ ထုတ်ယူမှုသေချာစေရန် ကျိုးကြောင်းဆီလျော်စွာ ထုတ်ယူမှုအပူချိန်နှင့် အရှိန်ကို ထိန်းချုပ်ပါ။
5. အထူးအခြေအနေများမှလွဲ၍ ကိရိယာနှင့် မှို၏မျက်နှာပြင်ပေါ်တွင် ဆီလိမ်းရန် တင်းကြပ်စွာတားမြစ်ထားသည်။
6. gasket ကို ကောင်းစွာ အအေးခံထားသည်။
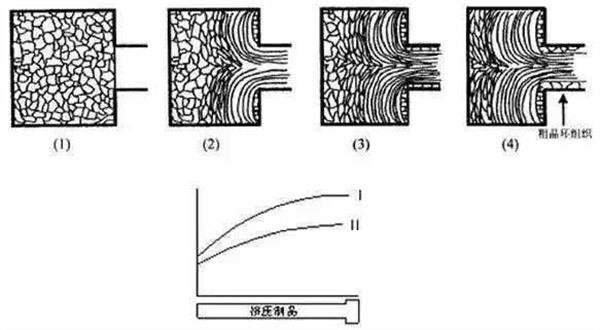
IIကြမ်းတမ်းသော ကြည်လင်သော လက်စွပ်
အလူမီနီယမ်အလွိုင်း extruded ထုတ်ကုန်အချို့သည် ကြမ်းသောစပါးကွင်းဟု ခေါ်သော အဖြေကို ကုသပြီးနောက် ထုတ်ကုန်၏ အစွန်အဖျားတစ်လျှောက်တွင် ကြမ်းသော ကောက်နှံဖွဲ့စည်းပုံ ဧရိယာကို ပေါင်းစပ်၍ ကြမ်းသောစပါးကွင်းဟုခေါ်သည် ။ထုတ်ကုန်များ၏ ကွဲပြားခြားနားသော ပုံသဏ္ဍာန်နှင့် လုပ်ဆောင်မှုနည်းလမ်းများကြောင့်၊ လက်စွပ်ပုံသဏ္ဌာန်၊ အကြမ်းထည်ပုံစံ နှင့် အခြားပုံစံများဖြင့် ပြုလုပ်ထားသော လက်စွပ်များကို ဖွဲ့စည်းနိုင်သည်။ကြမ်းသောလက်စွပ်၏အတိမ်အနက်သည် အမြီးမှ အရှေ့အထိ တဖြည်းဖြည်း လျော့နည်းလာပြီး လုံးဝပျောက်သွားသည်။ပင်မဖွဲ့စည်းပုံ ယန္တရားမှာ ပူပြင်းသော ထုတ်ယူပြီးနောက် ထုတ်ကုန်၏ မျက်နှာပြင်ပေါ်တွင် ဖွဲ့စည်းထားသော စပါးအခွဲဒေသဖြစ်ပြီး၊ ကြမ်းပြင်တွင် ပြန်လည်ပုံသွင်းထားသော ကောက်နှံဒေသကို အပူပေးခြင်းနှင့် ဖြေရှင်းချက်ဖြင့် ကုသပြီးနောက် ဖွဲ့စည်းသည်။
ကြမ်းတမ်းသော ကြည်လင်ခြင်း၏ အဓိကအကြောင်းအရင်းမှာ လက်စွပ်ဖြစ်သည်။
1. မညီညာသော extrusion ပုံပျက်ခြင်း။
2. အပူကုသမှု အပူချိန်သည် မြင့်မားပြီး ကောက်နှံများ ကြီးထွားလာစေရန် အချိန်ကြာရှည်စွာ ကိုင်ဆောင်ထားနိုင်ခြင်း၊
3. ရွှေ၏ ဓာတုဖွဲ့စည်းမှုမှာ ယုတ္တိမတန်ပါ။
4. ယေဘူယျအပူကုသနိုင်သော အားကောင်းစေသော သတ္တုစပ်များတွင် အပူကုသမှုပြီးနောက် ကြမ်းသောအကွင်းများပါရှိသည်။ အထူးသဖြင့် 6a02၊ 2a50 နှင့် အခြားသတ္တုစပ်များ၏ ပုံသဏ္ဍာန်များနှင့် အကန့်များသည် အပြင်းထန်ဆုံးဖြစ်ပြီး ဖယ်ရှား၍မရသည့်အပြင် အချို့သောအတိုင်းအတာအတွင်းသာ ထိန်းချုပ်နိုင်သည်။
5. extrusion ပုံသဏ္ဍာန်သည် သေးငယ်သည် သို့မဟုတ် ပုံပျက်ခြင်း မလုံလောက်ခြင်း၊ သို့မဟုတ် အရေးပါသော ပုံပျက်ခြင်းအကွာအဝေးတွင်ရှိပြီး ကြမ်းသောပုံဆောင်ခဲလက်စွပ်ကို ထုတ်လုပ်ရန် လွယ်ကူသည်။
ကာကွယ်နည်း
1. extrusion ဆလင်ဒါ၏ အတွင်းနံရံသည် ချောမွေ့သန့်ရှင်းပြီး ပွတ်တိုက်မှုအတွင်း ပွတ်တိုက်မှုကို လျှော့ချရန် ပြီးပြည့်စုံသော အလူမီနီယမ်လက်စွပ်ကို ဖွဲ့စည်းထားသည်။
2. ပုံပျက်ခြင်းအား တတ်နိုင်သမျှ ပြည့်ပြည့်စုံစုံနှင့် တစ်ပြေးညီဖြစ်သင့်ပြီး အပူချိန်နှင့် အရှိန်ကဲ့သို့သော လုပ်ငန်းစဉ်ဘောင်များကို ကျိုးကြောင်းဆီလျော်စွာ ထိန်းချုပ်သင့်သည်။
3. ဖြေရှင်းချက် ကုသမှု အပူချိန် မြင့်မားလွန်းခြင်း သို့မဟုတ် ကိုင်ဆောင်ချိန် အလွန်ကြာခြင်းကို ရှောင်ကြဉ်ပါ။
4. ပေါက်ပေါက်သေဆုံးနှင့်အတူ extrusion;
5. ပြောင်းပြန် extrusion method နှင့် static extrusion method ဖြင့် extrusion;
6. ဖြေရှင်းချက်-ပုံဆွဲ-အိုမင်းခြင်းနည်းလမ်းဖြင့် ထုတ်လုပ်သည်။
7. စုစုပေါင်းရွှေဖွဲ့စည်းမှုကို ချိန်ညှိပြီး ပြန်လည်ပုံသွင်းခြင်းအား တားဆီးသည့်ဒြပ်စင်ကို တိုးမြှင့်ပါ။
8. ပိုမိုမြင့်မားသောအပူချိန် extrusion ကိုသုံးပါ။
9. အချို့သောသတ္တုစပ်များသည် တစ်သားတည်းဖြစ်မနေကြဘဲ ကြမ်းသောစပါးကွင်းကို ထုတ်ယူချိန်တွင် တိမ်ကောနေပါသည်။
III, အလွှာ
၎င်းသည် သတ္တုစီးဆင်းမှုအတော်လေးတစ်ပြေးညီဖြစ်ပြီး မှိုနှင့် ရှေ့စွန်း elastic ဇုန်ကြားရှိ မျက်နှာပြင်ကြားရှိ ထုတ်ကုန်ထဲသို့ စီးဆင်းသွားသည့်အခါ ၎င်းသည် အရေပြားကွဲအက်ခြင်းချို့ယွင်းချက်ဖြစ်သည်။အလျားလိုက် အနိမ့်ချဲ့စမ်းသပ်မှုအပိုင်းတွင်၊ အပိုင်းဖြတ်ပိုင်း၏အစွန်းတွင် မတူညီသောအလွှာများ ချို့ယွင်းချက်ရှိနေပုံပေါ်သည်။
stratification ၏အဓိကအကြောင်းရင်း
1. မီးခိုး၏ မျက်နှာပြင်ပေါ်တွင် ဖုန်မှုန့်များ ရှိနေသည် သို့မဟုတ် အမှုန်အမွှားများသည် ကားအရေခွံ၊ သတ္တုအကျိတ်များအစား အလွှာများဖွဲ့စည်းရန် လွယ်ကူသော ကြီးမားသော အစုအဝေးများ ရှိနေသည် ။
2. ထုတ်ယူခြင်းမပြုမီ မသန့်စင်သော ဆီစွန်းထင်းမှု၊ လွှစာစသည်ဖြင့် အညစ်အကြေးများ သို့မဟုတ် အညစ်အကြေးများ မျက်နှာပြင်ပေါ်တွင် burrs များ ရှိပါသည်။
3. extrusion ဆလင်ဒါ၏အစွန်းနှင့်နီးကပ်သောသေဆုံးအပေါက်၏အနေအထားသည်ကျိုးကြောင်းဆီလျော်မှုမရှိပါ။
4. extrusion tool သည် ပြင်းထန်စွာ ဝတ်ဆင်ထားပြီး သို့မဟုတ် အချိန်မီ သန့်စင်၍ အစားထိုးမရနိုင်သော extrusion ဆလင်ဒါ၏ ချုံအတွင်း ဖုန်မှုန့်များ ရှိနေပါသည်။
5. extrusion pad ၏ အချင်း ကွာခြားချက်သည် ကြီးလွန်းသည်၊
6. extrusion ဆလင်ဒါ၏ အပူချိန်သည် ပေါက်၏ အပူချိန်ထက် များစွာ မြင့်မားသည်။
ကာကွယ်နည်း
1. မှိုများကို ကျိုးကြောင်းဆီလျော်စွာ ဒီဇိုင်းထုတ်ခြင်း၊ အချိန်မီ စစ်ဆေးခြင်းနှင့် အရည်အချင်းမပြည့်မီသော ကိရိယာများကို အစားထိုးခြင်း၊
2. အရည်အချင်းမပြည့်မီသော မီးဖိုထဲတွင် ထည့်သွင်းမထားပါ။
3. ကျန်ရှိသောပစ္စည်းကို ဖြတ်တောက်ပြီးနောက်၊ ချောဆီတွင် မကပ်ဘဲ သန့်စင်သင့်သည်။
4. extrusion ဆလင်ဒါ၏အဖုံးကို နဂိုအတိုင်းထားပါ၊ သို့မဟုတ် အဖုံးကို gasket ဖြင့် အချိန်မီ သန့်ရှင်းပါ။
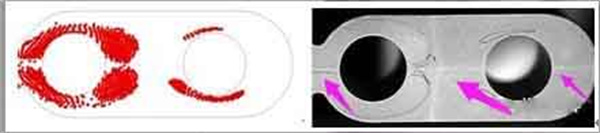
IVဂဟေဆက်ခြင်း ညံ့ဖျင်းခြင်း။
ဂဟေဆက်ရာတွင် ကွဲထွက်နေသော အခေါင်းပေါက်မှ ထုတ်လွှတ်သော ပစ္စည်း၏ ဂဟေဆက်ခြင်း သို့မဟုတ် မပြည့်စုံသော ဂဟေဆက်ခြင်းဖြစ်စဉ်ကို Weld welding ဟုခေါ်သည်။
ဂဟေဆက်ညံ့ခြင်း၏အဓိကအကြောင်းရင်း
1. extrusion coefficient သေးငယ်သည်၊ extrusion temperature နိမ့်သည်၊ extrusion speed မြန်သည်၊
2. Extrusion သိုးမွှေး သို့မဟုတ် ကိရိယာများသည် မသန့်ရှင်းပါ။
3. မှိုကိုဆီ;
4. မသင့်လျော်သောမှိုဒီဇိုင်း၊ မလုံလောက်သော သို့မဟုတ် ဟန်ချက်မညီသော hydrostatic ဖိအား၊ ကျိုးကြောင်းဆီလျော်မှုမရှိသော အပေါက်များဒီဇိုင်း
5. မီးဖိုမျက်နှာပြင်ပေါ်တွင် ဆီစွန်းထင်းနေပါသည်။
ကာကွယ်နည်း
1. extrusion coefficient၊ extrusion temperature နှင့် extrusion speed ကို စနစ်တကျ တိုးမြှင့်ပါ။
2. ကျိုးကြောင်းဆီလျော်သောဒီဇိုင်းနှင့် မှိုများထုတ်လုပ်ခြင်း၊
3. extrusion ဆလင်ဒါနှင့် extrusion gasket ကို ဆီမလိမ်းဘဲ သန့်ရှင်းအောင်ထားပါ။
4. သန့်ရှင်းသော မျက်နှာပြင်များဖြင့် ခွက်များကို အသုံးပြုပါ။
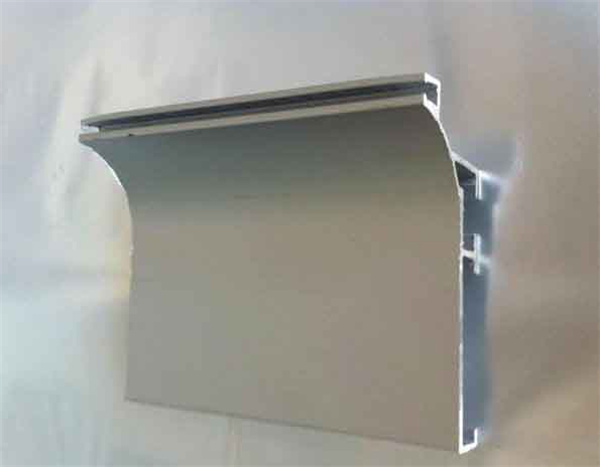
V. Extrusion အက်ကြောင်းများ
၎င်းသည် extruded ထုတ်ကုန်၏ transverse test အပိုင်း၏အစွန်းရှိ သေးငယ်သော arc ပုံသဏ္ဍာန်အက်ကွဲမှုဖြစ်ပြီး၊ အလင်းကိစ္စများတွင် epidermis အောက်တွင်ဝှက်ထားသော၊ ၎င်းသည် ၎င်း၏ longitudinal direction တစ်လျှောက်တွင် အချိန်အပိုင်းအခြားအလိုက် ကွဲအက်ကာ၊ အပြင်ဘက်အလွှာတွင် serrated အက်ကြောင်းများ ပြင်းထန်သော အခြေအနေများတွင်၊ သတ္တု၏ အဆက်ပြတ်မှုကို ဆိုးရွားစွာ ပျက်စီးစေသည်။extrusion လုပ်ငန်းစဉ်အတွင်း နံရံ၏ အချိန်အပိုင်းအခြားအလိုက် ဆန့်နိုင်အား လွန်ကဲစွာ ဖိစီးမှုကြောင့် သတ္တုမျက်နှာပြင်ကို ကွဲအက်သွားသောအခါ အက်ကြောင်းများ ဖြစ်ပေါ်လာသည်။
extrusion အက်ကြောင်း၏အဓိကအကြောင်းရင်း
1. extrusion speed က အရမ်းမြန်တယ်။
2. Extrusion အပူချိန် မြင့်မားလွန်းသည်။
3. extrusion speed သည် အလွန်အတက်အကျရှိသည်။
4. extruded သိုးမွှေး၏အပူချိန်မြင့်မားလွန်း;
5. ပေါက်ရောက်သောအသေကို extruded လုပ်သောအခါ၊ သေခြင်းအစီအစဉ်သည် ဗဟိုနှင့်နီးကပ်လွန်းသည်၊ ထို့ကြောင့် ဗဟိုသတ္တုထောက်ပံ့မှုမလုံလောက်သောကြောင့်၊ ဗဟိုနှင့်အစွန်းကြားစီးဆင်းမှုနှုန်းကွာခြားချက်မှာ ကြီးလွန်းသဖြင့်၊
6. ingot homogenization annealing သည် မကောင်းပါ။
ကာကွယ်နည်း
1. အမျိုးမျိုးသော အပူပေးခြင်းနှင့် ထုတ်ယူခြင်းဆိုင်ရာ သတ်မှတ်ချက်များကို တင်းကြပ်စွာ အကောင်အထည်ဖော်ပါ။
2. ပုံမှန်လည်ပတ်မှုရှိစေရန်အတွက် တူရိယာများနှင့် စက်ပစ္စည်းများကို မကြာခဏစစ်ဆေးခြင်း၊
3. မှိုဒီဇိုင်းကို ပြုပြင်မွမ်းမံပြီး ဂရုတစိုက်လုပ်ဆောင်ပါ၊ အထူးသဖြင့် မှိုတံတားဒီဇိုင်း၊ ဂဟေဆော်ခန်းနှင့် အစွန်းအချင်းအစရှိသော ကျိုးကြောင်းဆီလျော်မှုရှိသင့်သည်။
4. မြင့်မားသော မဂ္ဂနီဆီယမ် အလူမီနီယံသတ္တုစပ်များတွင် ဆိုဒီယမ်ပါဝင်မှုကို လျှော့ချပါ။
5. ၎င်း၏ပလတ်စတစ်နှင့် တစ်ပြေးညီဖြစ်တည်မှုကို တိုးတက်စေရန်အတွက် ingot ကို တစ်သားတည်းဖြစ်အောင်ပြုလုပ်ပြီး နှိမ့်ချထားသည်။
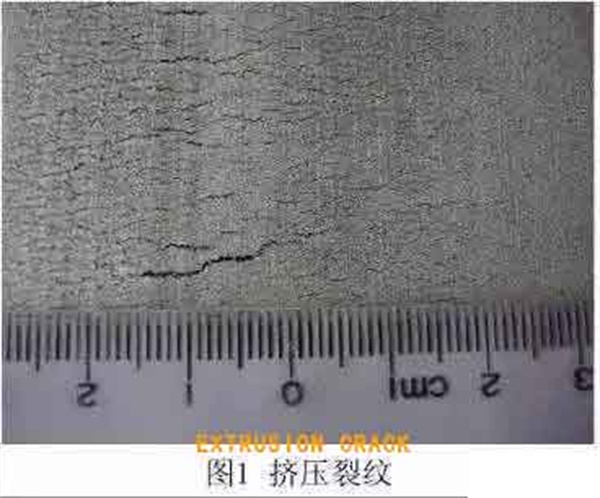
VI ။ပူဖောင်း
ဒေသတွင်း အရေပြားသတ္တုကို အခြေခံသတ္တုနှင့် အဆက်မပြတ် သို့မဟုတ် အဆက်မပြတ် ခွဲထုတ်ထားပြီး ၎င်းကို ပူဖောင်းဟုခေါ်သော စက်ဝိုင်းပုံသဏ္ဍာန်ရှိသော အပေါက်တစ်ခုအဖြစ် ထင်ရှားစေသည်။
ပူဖောင်းများဖြစ်ရခြင်း၏ အဓိကအကြောင်းရင်း
1. extruding လုပ်သောအခါ၊ extrusion ဆလင်ဒါနှင့် extrusion pad တွင် အစိုဓာတ်နှင့် ဆီကဲ့သို့သော အညစ်အကြေးများရှိသည်။
2. extrusion ဆလင်ဒါ၏ ဝတ်ဆင်မှုကြောင့်၊ ပွန်းပဲ့သောအစိတ်အပိုင်းနှင့် ingot အကြားလေသည် ထုထည်အတွင်း သတ္တုမျက်နှာပြင်အတွင်းသို့ ဝင်ရောက်သည်။
3. ချောဆီတွင် အစိုဓာတ်ရှိနေသည်၊
4. ingot ဖွဲ့စည်းပုံကိုယ်တိုင်က လျော့ရဲပြီး porosity ချို့ယွင်းချက်ရှိပါတယ်။
5. အပူကုသမှုအပူချိန် မြင့်မားလွန်းသည်၊ ကိုင်ဆောင်ချိန်က ရှည်လျားပြီး မီးဖိုအတွင်းရှိ လေထုစိုထိုင်းဆ မြင့်မားသည်။
6. ထုတ်ကုန်တွင် ဟိုက်ဒရိုဂျင်ပါဝင်မှု အလွန်မြင့်မားသည်။
7. Extrusion ဆလင်ဒါ အပူချိန် နှင့် ingot အပူချိန် မြင့်မားလွန်းသည်။
ကာကွယ်နည်း
1. ကိရိယာတန်ဆာပလာများ၏ မျက်နှာပြင်များကို သန့်ရှင်း၊ ချောမွတ်ပြီး ခြောက်သွေ့အောင် ထိန်းသိမ်းထားသင့်သည်။
2. Extrusion cylinder နှင့် extrusion gasket ၏ အရွယ်အစားကို ကျိုးကြောင်းဆီလျော်စွာ ဒီဇိုင်းဆွဲပါ၊ ကိရိယာ၏ အရွယ်အစားကို မကြာခဏ စစ်ဆေးပါ၊ ဗိုက်ကြီးသောအချိန်တွင် extrusion ဆလင်ဒါကို အချိန်မီ ပြုပြင်ပါ၊ နှင့် extrusion gasket သည် ခံနိုင်ရည်မရှိသင့်ပါ။
3. ချောဆီသည် သန့်ရှင်းခြောက်သွေ့ကြောင်း သေချာပါစေ။
4. ထုတ်ယူခြင်းလုပ်ငန်းစဉ်ကို တင်းတင်းကျပ်ကျပ်လိုက်နာပါ၊ အိတ်ဇောကို အချိန်မီဖြတ်ပါ၊ မှန်ကန်စွာဖြတ်ပါ၊ ဆီမလိမ်းပါနှင့်၊ ကျန်ရှိသောပစ္စည်းများကို လုံးဝဖယ်ရှားပါ၊ ကွက်လပ်များနှင့် မှိုများကို သန့်ရှင်းစေပြီး မညစ်ညမ်းစေပါ။
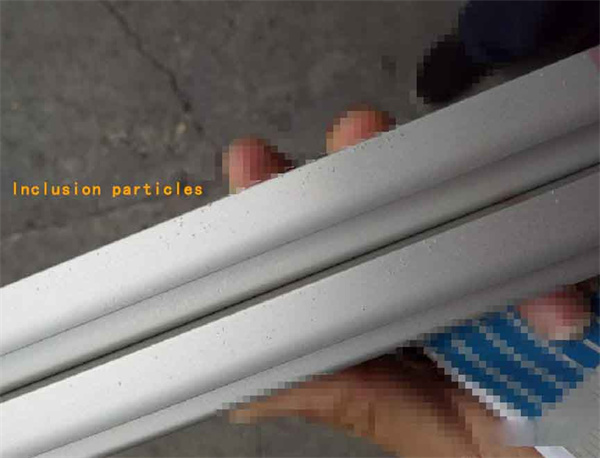
တင်ပြလာတဲ့အခွံခွာခြင်း။
ဤသည်မှာ အရေပြားသတ္တုနှင့် အလူမီနီယမ်သတ္တုစပ်ထုတ်ခြင်း ထုတ်ကုန်၏ အခြေခံသတ္တုတို့ကြား ပိုင်းခြားခြင်း၏ ဖြစ်စဉ်ဖြစ်သည်။
ကျွတ်ခြင်း၏အဓိကအကြောင်းရင်း
1. အလွိုင်းကို အစားထိုးပြီး extruded လုပ်သောအခါ၊ extrusion ဆလင်ဒါ၏ အတွင်းနံရံကို ကောင်းစွာ မသန့်စင်သော မူလသတ္တုဖြင့် ပြုလုပ်ထားသော ချုံပုတ်တွင် ကပ်ထားသည်။
2. extrusion ဆလင်ဒါနှင့် extrusion pad သည် မှန်ကန်စွာ ကိုက်ညီမှုမရှိပါ၊ နှင့် extrusion ဆလင်ဒါ၏ အတွင်းနံရံကို ဒေသအကြွင်းအကျန်သတ္တုဖြင့် စီတန်းထားပါသည်။
3. ၎င်းကို ချောဆီထုတ်သည့်ဆလင်ဒါဖြင့် extruded;
4. အသေအပေါက်တွင် သတ္တုရှိနေသည် သို့မဟုတ် အသေခံကြိုးသည် ရှည်လွန်းသည်။
ကာကွယ်နည်း
1. သတ္တုစပ်ကို extruded လုပ်သောအခါ extrusion ဆလင်ဒါကို သေချာစွာ သန့်စင်ပါ။
2. extrusion ဆလင်ဒါနှင့် extrusion gasket ၏ ကိုက်ညီသော အရွယ်အစားကို ကျိုးကြောင်းဆီလျော်စွာ ဒီဇိုင်းဆွဲပါ၊ tool size ကို မကြာခဏ စစ်ဆေးပါ၊ နှင့် extrusion gasket သည် သည်းမခံနိုင်တော့ပါ။
3. မှိုပေါ်ရှိ ကျန်သတ္တုများကို အချိန်မီရှင်းလင်းပါ။
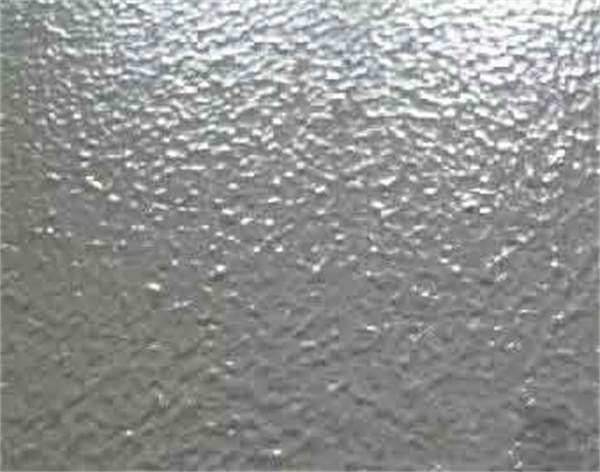
VIIIခြစ်ရာ
ချော်လဲနေစဉ်အတွင်း ချွန်ထက်သောအရာများနှင့် ထုတ်ကုန်၏မျက်နှာပြင်ကြား ထိတွေ့မှုကြောင့် ဖြစ်ပေါ်လာသော တစ်ခုတည်းသော အစင်းကြောင်းအမာရွတ်များကို ခြစ်ရာဟုခေါ်သည်။
ခြစ်မိခြင်း၏ အဓိကအကြောင်းရင်း
1. ကိရိယာတန်ဆာပလာများ မမှန်ကန်ခြင်း၊ ချောမွေ့မှုမရှိသော လမ်းညွန်များနှင့် အလုပ်စားပွဲများ၊ ချွန်ထက်သောထောင့်များ သို့မဟုတ် နိုင်ငံခြားအရာဝတ္ထုများ စသည်တို့။
2. မှိုလုပ်ငန်းသုံး ခါးပတ်ပေါ်တွင် သတ္တုပြားများ ရှိသည် သို့မဟုတ် မှိုလုပ်ငန်းခွင် ခါးပတ် ပျက်စီးသွားခြင်း၊
3. ချောဆီထဲတွင် သဲ သို့မဟုတ် သတ္တုကွဲပြားများပါရှိသည်။
4. သယ်ယူပို့ဆောင်ရေးကာလအတွင်း မသင့်လျော်သောလည်ပတ်မှုနှင့် မသင့်လျော်သောဖြန့်ကြက်မှု။
ကာကွယ်နည်း
1. မှိုအလုပ်လုပ်တဲ့ခါးပတ်ကို အချိန်မီစစ်ဆေးပြီး အရောင်တင်ပါ။
2. ထုတ်ကုန်၏ အထွက်လမ်းကြောင်းကို စစ်ဆေးပါ၊ ၎င်းသည် ချောမွေ့သင့်ပြီး လမ်းညွှန်လမ်းကြောင်းကို ကောင်းမွန်စွာ ချောဆီပေးနိုင်ပါသည်။
3. ကိုင်တွယ်စဉ်အတွင်း စက်ပိုင်းဆိုင်ရာ ပွတ်တိုက်ခြင်းနှင့် ခြစ်ခြင်းကို တားဆီးပါ။
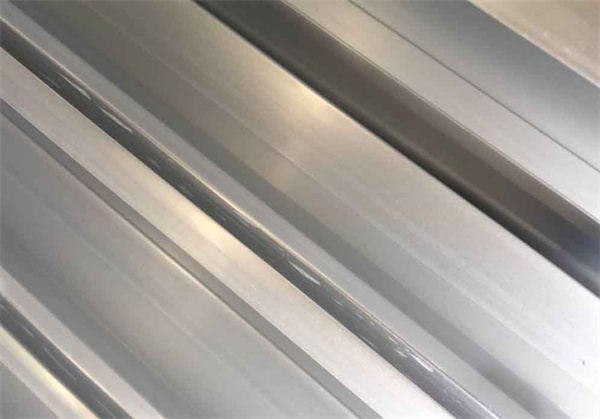
IXလာပြီး
ထုတ်ကုန်များ၏ မျက်နှာပြင်ပေါ်တွင် ဖြစ်ပေါ်လာသော အမာရွတ်များ သို့မဟုတ် အခြားအရာဝတ္ထုများနှင့် တိုက်မိသော အမာရွတ်များကို ဒဏ်ရာဟု ခေါ်သည်။
အဖုအကျိတ်ဖြစ်စေတဲ့ အဓိကအကြောင်းအရင်းပါ။
1. workbench နှင့် material rack ၏ဖွဲ့စည်းပုံသည် ယုတ္တိမရှိပေ။
2. ပစ္စည်းတင်းများ၊ ပစ္စည်းထုပ်များ စသည်တို့ကို မလျော်ကန်သော သတ္တုအကာအကွယ်၊
3. လည်ပတ်သည့်အခါ ဂရုတစိုက် မကိုင်တွယ်ပါနှင့်။
ကာကွယ်နည်း
1. ဂရုတစိုက်လုပ်ဆောင်ပါ၊ ဂရုတစိုက်ကိုင်တွယ်ပါ။
2. ချွန်ထက်သောထောင့်များကို ကြိတ်ချေပြီး ခြင်းတောင်းနှင့် ထိန်သိမ်းကို ပိုက်ကွန်နှင့် ပျော့ပျောင်းသောပစ္စည်းများဖြင့် ဖုံးအုပ်ပါ။
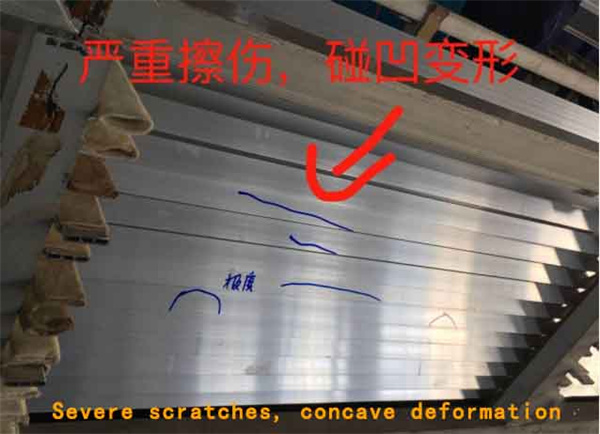
X. ခြစ်ရာများ
extruded ထုတ်ကုန်၏မျက်နှာပြင်သည် အစွန်းများ သို့မဟုတ် အခြားအရာဝတ္ထုများ၏ မျက်နှာပြင်များနှင့် ထိတွေ့မိပြီးနောက် ချော်လဲခြင်း သို့မဟုတ် နေရာရွှေ့ခြင်းကြောင့် ဖြစ်ပေါ်လာသော ထုတ်ကုန်၏မျက်နှာပြင်ပေါ်တွင် အစုအဝေးတွင် ပျံ့နှံ့နေသော အမာရွတ်များကို ခြစ်ရာဟုခေါ်သည်။
ခြစ်မိခြင်း၏ အဓိကအကြောင်းရင်း
1. မှိုကိုအလေးအနက်ထား;
2. သတ္တုတွင်း၏ အပူချိန်မြင့်မားမှုကြောင့်၊ အပေါက်သည် အလူမီနီယံတွင် ကပ်နေသောကြောင့် သို့မဟုတ် အပေါက်အတွင်း အလုပ်လုပ်သည့် ခါးပတ်များ ပျက်စီးသွားခြင်း၊
3. ဂရပ်ဖိုက်နှင့် ဆီကဲ့သို့သော အညစ်အကြေးများသည် ထုတ်ယူမှုဆလင်ဒါထဲသို့ ကျသွားသည်။
4. ထုတ်ကုန်များသည် တစ်ခုနှင့်တစ်ခု ရွေ့လျားနေသောကြောင့် မျက်နှာပြင်သည် ခြစ်မိပြီး extrusion flow သည် မညီမညာဖြစ်နေသောကြောင့် ထုတ်ကုန်များကို မျဉ်းဖြောင့်အတိုင်း မစီးဆင်းစေဘဲ ပစ္စည်းနှင့် လမ်းပြလမ်းကြောင်းနှင့် worktable ကြားတွင် ခြစ်ရာများဖြစ်ပေါ်စေပါသည်။
ကာကွယ်နည်း
1. အရည်အချင်းမရှိသောမှိုများကို အချိန်မီစစ်ဆေးပြီး အစားထိုးပါ။
2. သိုးမွှေး၏အပူအပူချိန်ကိုထိန်းချုပ်;
3. extrusion ဆလင်ဒါနှင့် သိုးမွှေး၏မျက်နှာပြင်သည် သန့်ရှင်းခြောက်သွေ့ကြောင်း သေချာပါစေ။
4. တူညီသောအမြန်နှုန်းကိုသေချာစေရန် extrusion speed ကိုထိန်းချုပ်ပါ။
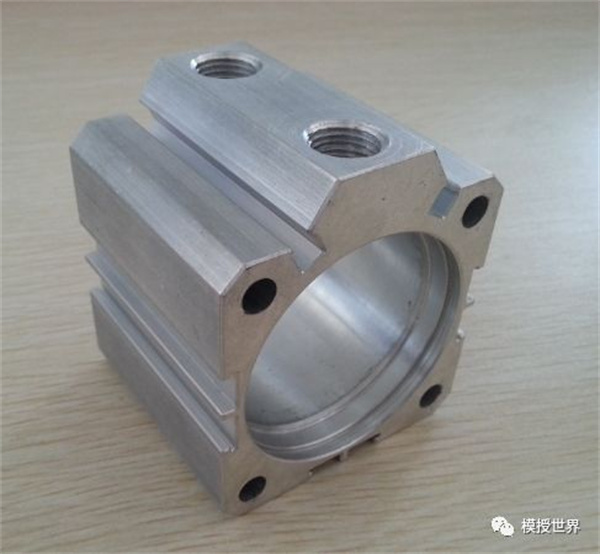
လာစရာ။မှိုအမှတ်အသား
၎င်းသည် extruded ထုတ်ကုန်၏မျက်နှာပြင်ပေါ်ရှိ အရှည်လိုက်မညီညာမှု၏ သဲလွန်စတစ်ခုဖြစ်ပြီး extruded ထုတ်ကုန်များအားလုံးသည် ဒီဂရီအမျိုးမျိုးအထိ သေဆုံးသည့်အမှတ်များရှိသည်။
မှိုတက်ခြင်း၏အဓိကအကြောင်းရင်း
အဓိကအကြောင်းရင်း- မှိုအလုပ်လုပ်သောခါးပတ်သည် လုံးဝချောမွေ့မှုကို မရရှိနိုင်ပါ။
ကာကွယ်နည်း
1. မှိုအလုပ်လုပ်သောခါးပတ်၏မျက်နှာပြင်သည် သန့်ရှင်းချောမွေ့ပြီး ချွန်ထက်သောအစွန်းများကင်းကြောင်း သေချာပါစေ။
2. မြင့်မားသောမျက်နှာပြင်မာကျောမှုသေချာစေရန်ကျိုးကြောင်းဆီလျော်စွာနိုက်ထရစ်ဒင်းကုသမှု;
3. မှိုကို မှန်ကန်စွာ ပြုပြင်ပါ။
4. အလုပ်လုပ်သည့်ခါးပတ်ကို ကျိုးကြောင်းဆီလျော်စွာ ဒီဇိုင်းထုတ်သင့်ပြီး အလုပ်လုပ်သည့်ခါးပတ်သည် အလွန်ရှည်သင့်သည်။
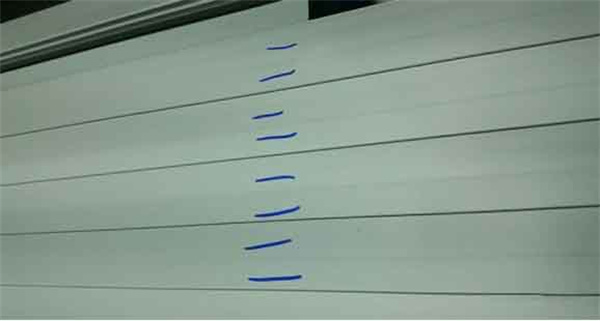
XIIလိမ်၊ ကွေး၊ လှိုင်း
extruded ထုတ်ကုန်၏ဖြတ်ပိုင်းကို အရှည်လိုက် ဦးတည်ရာသို့ ထောင့်ချိုးကွေ့သွားသည့်ဖြစ်စဉ်ကို လိမ်ခြင်းဟုခေါ်သည်။ထုတ်ကုန်ကို အလျားလိုက် ဦးတည်ရာသို့ ကွေးသွားခြင်း သို့မဟုတ် ဓားပုံသဏ္ဍာန် ဖြောင့်ဖြောင့်မဟုတ်သော ဖြစ်စဉ်ကို ကွေးခြင်းဟုခေါ်သည်။ထုတ်ကုန်၏ longitudinal direction တွင် ဖြစ်ပေါ်သည့် စဉ်ဆက်မပြတ် တုန်ခါနေသော ဖြစ်စဉ်ကို wave ဟုခေါ်သည်။
လိမ်ခြင်း၊ ကွေးခြင်းနှင့် လှိုင်းများဖြစ်ရခြင်း၏ အဓိကအကြောင်းရင်းများ
1. အသေပေါက်များ ၏ ဒီဇိုင်း နှင့် အစီအစဥ် သည် မကောင်း ၊ သို့မဟုတ် အလုပ် ခါးပတ် ၏ အရွယ်အစား သည် ကျိုးကြောင်းဆီလျော်မှု မရှိဘဲ၊
2. အသေပေါက်များ၏ စက်ပိုင်းဆိုင်ရာ တိကျမှု ညံ့ဖျင်းခြင်း၊
3. သင့်လျော်သောလမ်းညွှန်ကို မတပ်ဆင်ပါ။
4. မသင့်လျော်သောမှိုပြုပြင်မှု;
5. မသင့်လျော်သော extrusion အပူချိန်နှင့်မြန်နှုန်း;
6. ဖြေရှင်းချက်မကုသမီ ထုတ်ကုန်ကို ဖြောင့်ဖြောင့်မထားပါ။
7. အွန်လိုင်း အပူကုသစဉ်အတွင်း မညီမညာ အအေးခံခြင်း။
ကာကွယ်နည်း
1. မှိုဒီဇိုင်းနှင့်ကုန်ထုတ်လုပ်မှုအဆင့်မြင့်;
2. သင့်လျော်သော လမ်းညွှန်၊ ဆွဲငင်အားနှင့် ထုတ်ယူခြင်းကို ထည့်သွင်းပါ။
3. ဒေသတွင်း ချောဆီ၊ မှိုပြုပြင်ခြင်းနှင့် လွှဲခြင်းကို အသုံးပြုပါ သို့မဟုတ် သတ္တုစီးဆင်းမှုနှုန်းကို ချိန်ညှိရန်အတွက် shunt အပေါက်၏ ဒီဇိုင်းကို ပြောင်းလဲပါ။
4. ပုံသဏ္ဍာန်ပိုမိုတူညီစေရန်အတွက် extrusion temperature နှင့် speed ကို ကျိုးကြောင်းဆီလျော်စွာ ချိန်ညှိပါ။
5. သင့်လျော်သောဖြေရှင်းချက်ကုသမှုအပူချိန်ကိုလျှော့ချသို့မဟုတ်ဖြေရှင်းချက်ကုသမှုအတွက်ရေအပူချိန်ကိုတိုးမြှင့်;
6. အွန်လိုင်းမီးငြှိမ်းနေစဉ်အတွင်း တစ်ပြေးညီအအေးခံကြောင်း သေချာပါစေ။
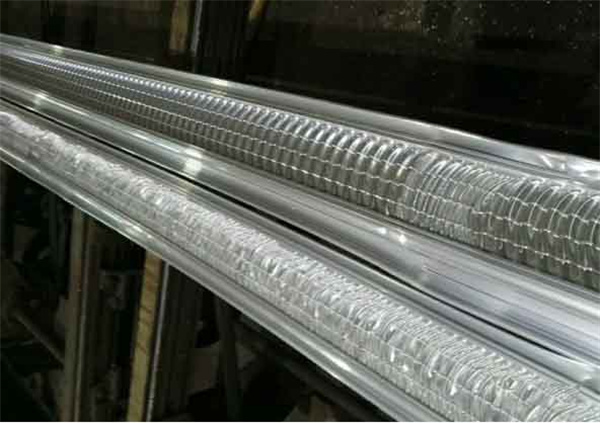
XIIIကိုင်းခက်
အလျား ဦးတည်ရာ တစ်နေရာရာမှာ ရုတ်ချည်း ကွေးညွှတ်နေတဲ့ ထုတ်ကုန်ကို ခဲကွေးခြင်းလို့ ခေါ်ပါတယ်။
ခက်ခက်ခဲခဲ ကွေးညွှတ်ရခြင်း၏ အဓိက အကြောင်းရင်း
1. မညီညာသော extrusion speed၊ အနိမ့်အမြန်နှုန်းမှ မြင့်မားသောအမြန်နှုန်းသို့ ရုတ်တရက်ပြောင်းလဲခြင်း သို့မဟုတ် အရှိန်မြင့်မှ အနိမ့်အမြန်နှုန်းသို့ ရုတ်တရက်ပြောင်းလဲခြင်းနှင့် ရုတ်တရတ်ရပ်တန့်ခြင်း၊
2. ထုတ်ယူခြင်းလုပ်ငန်းစဉ်အတွင်း ထုတ်ကုန်ကို တင်းတင်းကျပ်ကျပ် ရွှေ့ပါ။
3. extruder ၏ အလုပ်လုပ်သော မျက်နှာပြင်သည် မညီညာပါ။
ကာကွယ်နည်း
1. ကျပန်းဖြင့် မရပ်ပါနှင့် သို့မဟုတ် ထုတ်ယူမှု အရှိန်ကို ရုတ်တရက် မပြောင်းလဲပါနှင့်။
2. ပရိုဖိုင်ကို လက်ဖြင့် ရုတ်တရက် မရွှေ့ပါနှင့်။
3. discharge table သည် ပြားချပ်နေပြီး discharge roller table သည် နိုင်ငံခြားအရာမရှိဘဲ ချောမွေ့နေပြီး ပေါင်းစပ်ထုတ်ကုန်သည် အဟန့်အတားမရှိကြောင်း သေချာပါစေ။
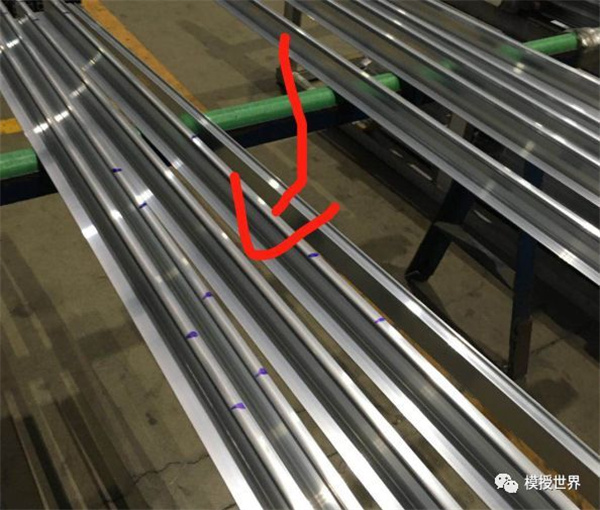
XIVကောက်ညှင်းခေါက်ဆွဲ
ဤသည်မှာ extruded ထုတ်ကုန်၏ မျက်နှာပြင် ချို့ယွင်းချက်ဖြစ်သည်၊ ဆိုလိုသည်မှာ ထုတ်ကုန်၏ မျက်နှာပြင်သည် အဆက်မပြတ် အဖုအပိန့်များ၊ အစက်အပြောက်များ ခြစ်ရာများ၊ တွင်းများ၊ သတ္တုစေ့များ စသည်တို့သည် သေးငယ်သော မညီမညာဖြစ်နေသည်။
pockmark ၏အဓိကအကြောင်းရင်း
1. မှို၏ မာကျောမှု မလုံလောက်ခြင်း သို့မဟုတ် မာကျောမှု မညီညာခြင်း၊
2. Extrusion အပူချိန် မြင့်မားလွန်းသည်။
3. extrusion speed က အရမ်းမြန်တယ်။
4. မှို၏အလုပ်လုပ်သောခါးပတ်သည် ရှည်လွန်း၍ ကြမ်းတမ်းသော သို့မဟုတ် သတ္တုဖြင့် ကပ်နေခြင်း၊
5. extruded သိုးမွှေးသည် ရှည်လွန်းသည်။
ကာကွယ်နည်း
1. မှိုလုပ်ငန်းခွင် ခါးပတ်၏ မာကျောမှုနှင့် မာကျောမှု တူညီမှုကို မြှင့်တင်ပါ။
2. စည်းမျဉ်းများနှင့်အညီ extrusion ဆလင်ဒါနှင့် ingot ကို အပူပေးပြီး သင့်လျော်သော extrusion speed ကို အသုံးပြုပါ။
3. မှိုကို ကျိုးကြောင်းဆီလျော်စွာ ဒီဇိုင်းဆွဲပါ၊ အလုပ်လုပ်သော ခါးပတ်၏ မျက်နှာပြင်ကြမ်းတမ်းမှုကို လျှော့ချပြီး မျက်နှာပြင် စစ်ဆေးခြင်း၊ ပြုပြင်ခြင်းနှင့် ပေါလစ်တိုက်ခြင်းတို့ကို အားကောင်းစေခြင်း၊
4. သင့်လျော်သော ingot အရှည်ကိုသုံးပါ။
XVသတ္တုနှိပ်ခြင်း။
extrusion လုပ်ငန်းစဉ်အတွင်း၊ metal chips များကို metal pressing ဟုခေါ်သော ထုတ်ကုန်၏မျက်နှာပြင်သို့ ဖိထားသည်။
သတ္တုဝင်ရောက်မှု၏ အဓိကအကြောင်းရင်းများ
1. သိုးမွှေးစွန်းများသည် မှားယွင်းနေပါသည်။
2. သိုးမွှေး၏ အတွင်းမျက်နှာပြင်သည် သတ္တုဖြင့် ကပ်နေပြီး သို့မဟုတ် ချောဆီတွင် သတ္တုအပျက်အစီးများနှင့် အခြားအညစ်အကြေးများပါရှိသည်။
3. extrusion ဆလင်ဒါကို မသန့်စင်ဘဲ၊ အခြားသတ္တုအပျက်အစီးများပါရှိပါသည်။
4. ingot သည် အခြားသော သတ္ထု နိုင်ငံခြားအရာဝတ္ထုများထဲသို့ နစ်မြုပ်နေပါသည်။
5. သိုးမွှေးတွင် slag ပါ၀င်သည်။
ကာကွယ်နည်း
1. သိုးမွှေးပေါ်ရှိ burrs များကိုဖယ်ရှားပါ။
2. သိုးမွှေး၏မျက်နှာပြင်နှင့် ချောဆီသည် သန့်ရှင်းခြောက်သွေ့ကြောင်း သေချာပါစေ။
3. မှိုနှင့် extrusion ဆလင်ဒါရှိ သတ္တုအပျက်အစီးများကို သန့်စင်ပါ။
4. အရည်အသွေးမြင့် သိုးမွှေးကို ရွေးချယ်ပါ။
XVIသတ္တုမဟုတ်သောနှိပ်ခြင်း။
ကျောက်အနက်ရောင်ကဲ့သို့သော နိုင်ငံခြားအရာများကို extruded ထုတ်ကုန်၏ အတွင်းနှင့် အပြင်မျက်နှာပြင်များသို့ ဖိထားပြီး၊ သတ္တုမဟုတ်သော indentation ဟုခေါ်သည်။ပြင်ပအရာများကို ဖယ်ထုတ်ပြီးနောက်၊ ထုတ်ကုန်၏ အတွင်းမျက်နှာပြင်သည် ကွဲပြားသော အရွယ်အစားများကို ပြသမည်ဖြစ်ပြီး၊ ထုတ်ကုန်၏ မျက်နှာပြင်၏ အဆက်ပြတ်မှုကို ပျက်ပြားစေမည်ဖြစ်သည်။
သတ္တုမဟုတ်သော ကျူးကျော်ဝင်ရောက်ခြင်း၏ အဓိကအကြောင်းရင်း
1. ဂရပ်ဖိုက်အမှုန်အမွှား အရွယ်အစားသည် အစိုဓာတ် သို့မဟုတ် ဆီများ ပါဝင်သော ကြမ်း သို့မဟုတ် စုစည်းကာ မွှေပြီး မညီမညာဖြစ်နေသည်။
2. ဆလင်ဒါဆီ၏ flash point သည် နည်းပါသည်။
3. ဆလင်ဒါဆီနှင့် ဂရပ်ဖိုက်အချိုးမလျော်ညီ၍ ဂရပ်ဖိုက်များလွန်းသည်။
ကာကွယ်နည်း
1. အရည်အသွေးပြည့်မီသော ဂရပ်ဖိုက်ကို အသုံးပြု၍ ခြောက်သွေ့အောင်ထားပါ။
2. အရည်အချင်းပြည့်မီသောချောဆီများကို စစ်ထုတ်ပြီး အသုံးပြုပါ။
3. ချောဆီနှင့် ဂရပ်ဖိုက်အချိုးကို ထိန်းချုပ်ပါ။
XVIIမျက်နှာပြင်ချေး
မျက်နှာပြင် ကုသမှု မခံယူရသေးသော Extruded ထုတ်ကုန်များ၊ extruded ထုတ်ကုန်၏ မျက်နှာပြင်သည် ပြင်ပကြားခံနှင့် ဓာတု သို့မဟုတ် လျှပ်စစ်ဓာတ် တုံ့ပြန်မှုပြီးနောက်၊ မျက်နှာပြင် ချေးချွတ်ခြင်းဟုခေါ်သော မျက်နှာပြင်၏ ဒေသဆိုင်ရာ ပျက်စီးမှုကြောင့် ချို့ယွင်းချက် ဖြစ်စေသည်။သံချေးတက်နေသော ထုတ်ကုန်၏ မျက်နှာပြင်သည် ၎င်း၏ သတ္တုတောက်ပြောင်မှု ဆုံးရှုံးသွားပြီး ပြင်းထန်သော အခြေအနေများတွင် မီးခိုးရောင်-အဖြူရောင် ချေးထုတ်သည့် ထုတ်ကုန်များကို မျက်နှာပြင်ပေါ်တွင် ထုတ်လုပ်ပါသည်။
မျက်နှာပြင်ချေး၏အဓိကအကြောင်းရင်း
1. ထုတ်ကုန်သည် ထုတ်လုပ်ခြင်း၊ သိုလှောင်ခြင်းနှင့် သယ်ယူပို့ဆောင်စဉ်အတွင်း ရေ၊ အက်ဆစ်၊ အယ်လကာလီ၊ ဆားစသည့် အဆိပ်သင့်သောမီဒီယာနှင့် ထိတွေ့ခြင်း သို့မဟုတ် စိုစွတ်သောလေထုတွင် အချိန်ကြာမြင့်စွာ ရပ်ထားခြင်းဖြစ်သည်။
2. မသင့်လျော်သောသတ္တုစပ်ဖွဲ့စည်းမှုအချိုး;
ကာကွယ်နည်း
1. ထုတ်ကုန်မျက်နှာပြင်နှင့် ထုတ်လုပ်မှုနှင့် သိုလှောင်မှုပတ်ဝန်းကျင်ကို သန့်ရှင်းခြောက်သွေ့အောင်ထားပါ။
2. အလွိုင်းအတွင်းရှိ ဒြပ်စင်များ ပါဝင်မှုကို ထိန်းချုပ်ပါ။
XVIIIလိမ္မော်ခွံ
extruded ထုတ်ကုန်၏မျက်နှာပြင်တွင် မျက်နှာပြင်အရေးအကြောင်းဟုလည်းသိကြသော လိမ္မော်ခွံကဲ့သို့ မညီညာသော အရေးအကြောင်းများရှိသည်။၎င်းသည် ထုတ်ယူစဉ်အတွင်း အစေ့အဆန်ကြမ်းများကြောင့် ဖြစ်ရသည်။အစေ့အဆန်တွေ ပိုကြမ်းလေ အရေးအကြောင်းတွေ ပိုသိသာလာပါတယ်။
လိမ္မော်ခွံ၏အဓိကအကြောင်းရင်း
1. ingot ဖွဲ့စည်းပုံသည် မညီမညာဖြစ်ပြီး တစ်သားတည်းဖြစ်စေသော ကုသမှုသည် မလုံလောက်ပါ။
2. ထုတ်ယူမှုအခြေအနေများသည် ကျိုးကြောင်းဆီလျော်မှုမရှိသည့်အပြင် အချောထည်ပစ္စည်းများ၏ အစေ့အဆန်များသည် ကြမ်းသည်။
3. ဆန့်ခြင်းနှင့် ဖြောင့်ခြင်းပမာဏသည် ကြီးမားလွန်းသည်။
ကာကွယ်နည်း
1. တစ်သားတည်းဖြစ်ခြင်းလုပ်ငန်းစဉ်ကို ကျိုးကြောင်းဆီလျော်စွာ ထိန်းချုပ်ပါ။
2. ပုံပျက်ခြင်းကို တတ်နိုင်သမျှ တူညီနေသင့်သည် (extrusion temperature, speed, etc.)
3. တင်းမာမှု တည့်မတ်မှု ပမာဏကို အရမ်းကြီး မကြီးမားအောင် ထိန်းချုပ်ပါ။
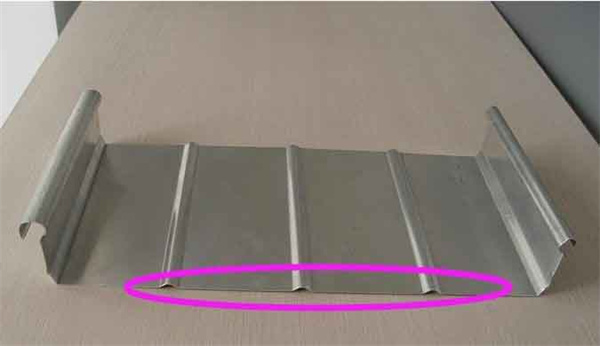
XIXမညီမညာ
ထုတ်ယူပြီးနောက်၊ လေယာဉ်ပေါ်ရှိ ထုတ်ကုန်၏အထူသည် ပြောင်းလဲသွားသည့် ဧရိယာသည် အဝိုက် သို့မဟုတ် ခုံးပုံပေါ်သည်။ယေဘူယျအားဖြင့်တော့ သာမန်မျက်စိနဲ့ ကြည့်လို့မရပါဘူး။မျက်နှာပြင်ကို ကုသပြီးနောက်တွင် အရိပ်ကောင်းများ သို့မဟုတ် အရိုးအရိပ်များ ပေါ်လာသည်။
မညီမညာဖြစ်ရခြင်း၏ အဓိကအကြောင်းအရင်းဖြစ်သည်။
1. မှိုအလုပ်လုပ်သောခါးပတ်သည် မှန်ကန်စွာ ဒီဇိုင်းမွမ်းမံထားခြင်းဖြစ်ပြီး မှိုပြုပြင်မှုမှာ နေရာမရှိပေ။
2. shunt hole သို့မဟုတ် pre-chamber ၏အရွယ်အစားသည် မသင့်လျော်ဘဲ၊ ဖြတ်ကျော်ဧရိယာရှိ ပရိုဖိုင်ကို ဆွဲခြင်း သို့မဟုတ် ချဲ့ခြင်း၏ အင်အားသည် လေယာဉ်အတွင်း အနည်းငယ်ပြောင်းလဲမှုကို ဖြစ်စေသည်။
3. အအေးပေးခြင်းလုပ်ငန်းစဉ်သည် မညီမညာဖြစ်ပြီး ထူထဲသောနံရံများ သို့မဟုတ် လမ်းဆုံအပိုင်း၏ အအေးခံမှုအရှိန်နှေးကွေးကာ အအေးခံသည့်လုပ်ငန်းစဉ်အတွင်း လေယာဉ်၏ ကွဲပြားသောဒီဂရီများ ကျုံ့သွားကာ ပုံပျက်သွားခြင်း၊
4. အထူ၏ကြီးမားသောကွာခြားမှုကြောင့်၊ ထူထဲသောနံရံအစိတ်အပိုင်း သို့မဟုတ် အသွင်ကူးပြောင်းရေးနယ်မြေအဖွဲ့အစည်းနှင့် အဖွဲ့အစည်း၏အခြားအစိတ်အပိုင်းများကြား ခြားနားချက်တိုးလာပါသည်။
ကာကွယ်နည်း
1. မှိုဒီဇိုင်း၊ ထုတ်လုပ်ခြင်းနှင့် မှိုပြုပြင်ခြင်း အဆင့်ကို မြှင့်တင်ပါ။
2. ယူနီဖောင်းအအေးနှုန်းသေချာပါစေ။
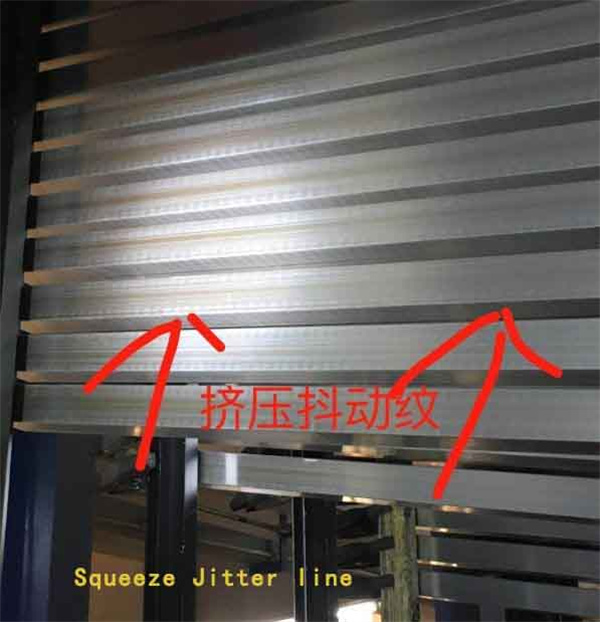
XXတုန်ခါမှုပုံစံ
၎င်းသည် extruded ထုတ်ကုန်၏မျက်နှာပြင်သို့ အချိန်အပိုင်းအခြားအလိုက် ချွတ်ယွင်းချက်တစ်ခုဖြစ်သည်။၎င်းသည် ထုတ်ကုန်၏မျက်နှာပြင်ပေါ်ရှိ အလျားလိုက် အဆက်မပြတ် အစင်းကြောင်းများဖြင့် သွင်ပြင်လက္ခဏာရှိပြီး အစင်းကြောင်းမျဉ်းကွေးသည် မှို၏အလုပ်လုပ်သောခါးပတ်၏ပုံသဏ္ဍာန်နှင့် ကိုက်ညီပြီး ပြင်းထန်သောကိစ္စများတွင် သိသာထင်ရှားသော ဗိုင်းရပ်ခံစားရမှုရှိသည်။
တုန်ခါမှု၏အဓိကအကြောင်းရင်း
1. extrusion shaft သည် ရှေ့သို့ရွေ့လျားပြီး သတ္တုကို အပေါက်ထဲမှ ထွက်လာသောအခါ လှုပ်ခါစေသည့် ပစ္စည်းကိရိယာ အကြောင်းရင်းများကြောင့် လှုပ်ခါခြင်း၊
2. မှိုကြောင့် သေတွင်းမှ သတ္တုသည် တုန်ခါသည်။
3. မှိုပံ့ပိုးမှု pad သည် သင့်လျော်မှုမရှိပါ၊ မှို၏တောင့်တင်းမှုမကောင်းပါ၊ နှင့် extrusion force သည် အတက်အကျရှိသောအခါ တုန်ခါမှုဖြစ်ပေါ်ပါသည်။
ကာကွယ်နည်း
1. အရည်အချင်းပြည့်မီသောမှိုများကိုသုံးပါ။
2. မှိုတပ်ဆင်သောအခါတွင် သင့်လျော်သော ထောက်ကူအကန့်များကို အသုံးပြုသင့်သည်။
3. စက်ကိရိယာကို ချိန်ညှိပါ။
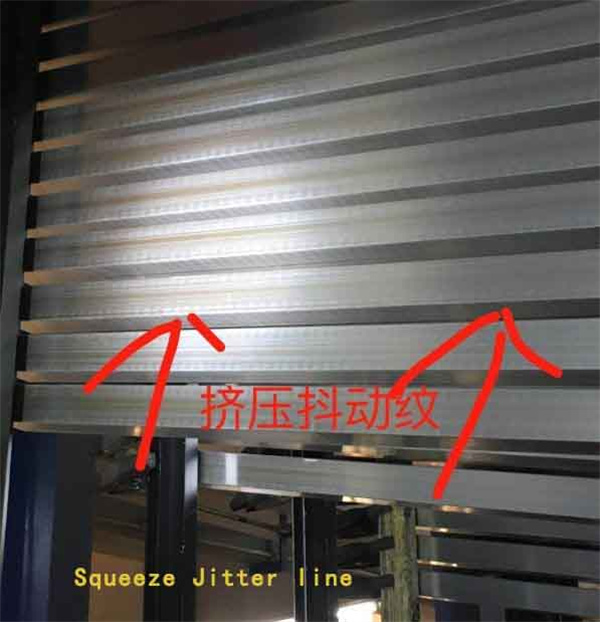
XXI၊ ရောနှော
ပါဝင်ရခြင်း၏ အဓိကအကြောင်းရင်း
ပါဝင်သည့် billet တွင် သတ္တု သို့မဟုတ် သတ္တုမဟုတ်သော ပါဝင်မှုများရှိသောကြောင့်၊ ၎င်းကို ယခင်လုပ်ထုံးလုပ်နည်းတွင် မတွေ့ရှိရဘဲ၊ ထုတ်ယူပြီးနောက် ထုတ်ကုန်၏ အတွင်း သို့မဟုတ် မျက်နှာပြင်ပေါ်တွင် ကျန်ရှိနေခဲ့သည်။
ကာကွယ်နည်း
သတ္တု သို့မဟုတ် သတ္တုမဟုတ်သော ပါဝင်မှုများပါရှိသော billet အား ထုတ်ယူခြင်းလုပ်ငန်းစဉ်သို့ ဝင်ရောက်ခြင်းမှ တားဆီးရန် billet ၏ စစ်ဆေးခြင်းကို အားကောင်းစေပါသည်။

XXII၊ ရေအမှတ်
ထုတ်ကုန်၏မျက်နှာပြင်ပေါ်ရှိ အဖြူဖျော့ သို့မဟုတ် အနက်ရောင်ဖျော့ဖျော့ပုံမမှန်သော ရေလိုင်းအမှတ်အသားများကို ရေအမှတ်အသားဟုခေါ်သည်။
ရေဓာတ်များရခြင်း၏ အဓိကအကြောင်းရင်း
1. သန့်စင်ပြီးနောက် အခြောက်ခံခြင်းသည် မကောင်းပါ၊ ထုတ်ကုန်၏ မျက်နှာပြင်ပေါ်တွင် ကျန်ရှိသော အစိုဓာတ်ရှိနေပါသည်။
2. မိုးရွာခြင်းနှင့် အခြားအကြောင်းများကြောင့် ဖြစ်ပေါ်လာသော ထုတ်ကုန်၏ မျက်နှာပြင်ပေါ်ရှိ ကျန်အစိုဓာတ်ကို အချိန်မီ မသန့်စင်နိုင်ခြင်း၊
3. အိုမင်းသောမီးဖို၏ လောင်စာတွင် ရေပါ၀င်ပြီး ထုတ်ကုန်၏ အအေးခံချိန်အတွင်း ထုတ်ကုန်၏မျက်နှာပြင်ပေါ်တွင် ရေများ စုပုံလာသည်။
4. အိုမင်းသောမီးဖို၏လောင်စာသည် မသန့်ရှင်းဘဲ၊ လောင်ကျွမ်းပြီးနောက်တွင် ဆာလဖာဒိုင်အောက်ဆိုက်ဓာတ်ငွေ့ကြောင့် သို့မဟုတ် ဖုန်မှုန့်များဖြင့် ညစ်ညမ်းသွားသည်။
၅။မီးငြိမ်းလတ်သော် ညစ်ညူး၏။
ကာကွယ်နည်း
1. ထုတ်ကုန်၏မျက်နှာပြင်ကို ခြောက်သွေ့သန့်ရှင်းအောင်ထားပါ။
2. အိုမင်းရင့်ရော်မှု၏ အစိုဓာတ်ပါဝင်မှုနှင့် သန့်ရှင်းမှုကို ထိန်းချုပ်ပါ။
3. quenching medium ၏စီမံခန့်ခွဲမှုကိုအားကောင်းစေပါ။
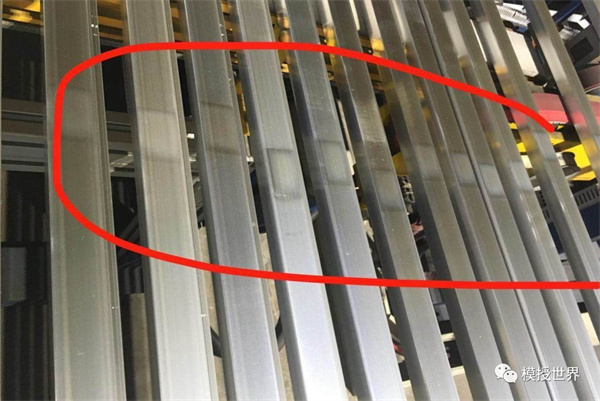
XXIIIကွာဟချက်
ပေတံကို extruded product ၏ လေယာဉ်ပျံတစ်ခုပေါ်တွင် အလျားလိုက် ခြုံထားပြီး ကွာဟမှုဟုခေါ်သော ပေတံနှင့် မျက်နှာပြင်ကြားတွင် ကွာဟချက်အချို့ရှိသည်။
ကွာဟမှု၏အဓိကအကြောင်းရင်း
သတ္တုထုတ်ခြင်း သို့မဟုတ် မလျော်ကန်သော အချောသပ်ခြင်း နှင့် ဖြောင့်ခြင်း လုပ်ငန်းဆောင်တာများအတွင်း မညီမညာသော သတ္တုစီးဆင်းမှု။
ကာကွယ်နည်း
မှိုများကို ကျိုးကြောင်းဆီလျော်စွာ ဒီဇိုင်းရေးဆွဲထုတ်လုပ်ခြင်း၊ မှိုပြုပြင်ခြင်းကို အားကောင်းစေခြင်း၊ စည်းမျဉ်းများနှင့်အညီ extrusion temperature နှင့် extrusion speed ကို တင်းကျပ်စွာ ထိန်းချုပ်ပါ။
XXIV၊ မညီညာသောနံရံအထူ
တူညီသောအရွယ်အစားရှိ Extruded ထုတ်ကုန်များသည် တူညီသောအပိုင်း သို့မဟုတ် အလျားလိုက်လမ်းကြောင်းရှိ ပါးလွှာသော သို့မဟုတ် ထူထဲသောနံရံများရှိပြီး ယင်းဖြစ်စဉ်ကို မညီညာသောနံရံအထူဟုခေါ်သည်။
နံရံအထူမညီမညာဖြစ်ရခြင်း၏ အဓိကအကြောင်းရင်း
1. မှိုဒီဇိုင်းသည် ကျိုးကြောင်းဆီလျော်မှုမရှိပါ၊ သို့မဟုတ် ကိရိယာနှင့် မှိုတပ်ဆင်ခြင်းသည် မသင့်လျော်ပါ။
2. extrusion ဆလင်ဒါ နှင့် extrusion needle တို့သည် တူညီသော အလယ်မျဉ်းပေါ်တွင် မဟုတ်ဘဲ eccentricity ကို ဖြစ်ပေါ်စေသည် ။
3. extrusion ဆလင်ဒါ၏အလွှာသည် အလွန်အကျွံ စုတ်ပြဲနေပြီး မှိုကို ခိုင်မြဲစွာ မပြုပြင်နိုင်သောကြောင့် eccentricity ကို ဖြစ်ပေါ်စေသည်၊
4. ပထမအကြိမ်နှင့်ဒုတိယအကြိမ်ထုတ်ခြင်းပြီးနောက် ingot ဗလာကိုယ်နှိုက်၏မညီမညာသောနံရံအထူကိုမဖယ်ရှားနိုင်ပါ။လှိမ့်၍ ဆန့်ပြီးနောက် သိုးမွှေး၏ မညီမညာသော နံရံအထူကို မဖယ်ရှားပါ။
5. ချောဆီသည် သတ္တုကို မညီမညာ စီးဆင်းစေသည်။
ကာကွယ်နည်း
1. ကိရိယာတန်ဆာပလာများနှင့် မှိုများ၏ ဒီဇိုင်းနှင့် ထုတ်လုပ်ခြင်းကို အကောင်းဆုံးဖြစ်အောင်၊ ဆင်ခြင်တုံတရားဖြင့် စုဝေးပြီး ချိန်ညှိပါ။
2. extruder ၏ဗဟိုကိုချိန်ညှိပြီး extrusion သေဆုံး;
3. အရည်အချင်းပြည့်မီသော ကွက်လပ်များကို ရွေးချယ်ပါ။
4. extrusion temperature၊ extrusion speed နှင့် အခြားသော process parameters များကို ကျိုးကြောင်းဆီလျော်စွာ ထိန်းချုပ်ပါ။
XXV(နှင့်) ပါးစပ်ကို ချဲ့သည်။
groove နှင့် I-shaped ကဲ့သို့သော extruded profile ထုတ်ကုန်များ၏ နှစ်ဖက်စလုံးသည် အပြင်ဘက်သို့ တိမ်းစောင်းသွားသော ချို့ယွင်းချက်ကို flaring ဟုခေါ်ပြီး အတွင်းဘက်သို့ စောင်းနေသော ချို့ယွင်းချက်ကို parallel opening ဟုခေါ်သည်။
ချဲ့ထွင်ခြင်း (consolidation) ၏ အဓိက အကြောင်းရင်းများ၊
1. ကျင်း သို့မဟုတ် အလားတူ ကျင်းပရိုဖိုင်များ သို့မဟုတ် I-shaped ပရိုဖိုင်များ၏ သတ္တုစီးနှုန်းသည် မညီမညာဖြစ်နေသည်။
2. groove အောက်ခြေပန်းကန်၏နှစ်ဖက်စလုံးရှိအလုပ်လုပ်ခါးပတ်၏စီးဆင်းမှုနှုန်းမညီမညာဖြစ်;
3. မသင့်လျော်သောဆန့်ဖြောင့်စက်;
4. ထုတ်ကုန်သည် မှိုပေါက်ထဲမှ ထွက်ပြီးနောက်၊ အွန်လိုင်းဖြေရှင်းချက် ကုသမှုသည် ညီညာစွာ အေးသွားပါသည်။
ကာကွယ်နည်း
1. extrusion speed နှင့် extrusion temperature ကို တင်းကျပ်စွာ ထိန်းချုပ်ပါ။
2. အအေး၏တူညီမှုကိုသေချာစေပါ။
3. မှိုများကို မှန်ကန်စွာ ဒီဇိုင်းဆွဲပြီး ထုတ်လုပ်ခြင်း၊
4. extrusion temperature နှင့် speed ကို တင်းကျပ်စွာ ထိန်းချုပ်ပြီး tool ကို တပ်ဆင်ပြီး မှန်ကန်စွာ သေဆုံးစေပါသည်။
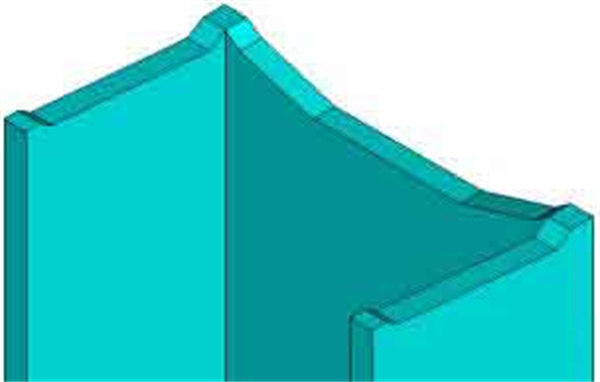
XXVIဖြောင့်တန်းမှုအမှတ်အသား
extruded ထုတ်ကုန်၏အပေါ်ပိုင်းအလိပ်ကို ဖြောင့်တန်းသည့်အခါ ထွက်လာသော helical streaks များကို straightening marks ဟုခေါ်ပြီး အထက်လိပ်ဖြင့် ဖြောင့်ထားသော မည်သည့်ထုတ်ကုန်အတွက်မဆို ဖြောင့်တန်းခြင်းအမှတ်အသားများကို ရှောင်ရှား၍မရပါ။
ဖြောင့်တန်းခြင်း၏အဓိကအကြောင်းရင်း
1. ဖြောင့်စက်၏ ဒလိမ့်တုံးမျက်နှာပြင်ပေါ်တွင် အစွန်းများရှိပါသည်။
2. ထုတ်ကုန်၏ကွေးညွှတ်မှုအလွန်ကြီးမားသည်;
3. အလွန်အကျွံဖိအား;
4. ဖြောင့်စက်၏ ထောင့်သည် ကြီးလွန်းသည်။
5. ထုတ်ကုန်သည် ကြီးမားသော ဘဲဥပုံရှိသည်။
ကာကွယ်နည်း
အကြောင်းတရားအလိုက် သင့်လျော်သောအစီအမံများကို ဆောင်ယူပါ။
XXVIIမှတ်တိုင်များ၊ ချက်ခြင်းအထင်အမြင်များ၊ ကိုက်မှတ်များ
ကုန်ပစ္စည်း၏မျက်နှာပြင်ပေါ်ရှိ အစင်းကြောင်းများထွက်စေရန်နှင့် ရပ်တန့်ခြင်းအမှတ်အသားဟုခေါ်သော ထုတ်ယူမှုဦးတည်ချက်ဆီသို့ ကန့်လန့်ကန့်လန့်ဖြတ်ထုတ်နေစဉ်အတွင်း extrusion ကိုရပ်ပါ။ထုတ်ကုန်၏မျက်နှာပြင်ပေါ်ရှိ မျဉ်းကြောင်းများ သို့မဟုတ် အစင်းကြောင်းများ ထုတ်ယူနေစဉ်အတွင်း ထုတ်ယူမှုလမ်းကြောင်းနှင့် ထောင့်မှန်အကိုက်ခံရသော အမှတ်အသားများ သို့မဟုတ် လက်ငင်းအထင်အမြင်များ ("အတုပါကင်အမှတ်များ" ဟုလူသိများသည်)
ထုတ်ယူစဉ်အတွင်း၊ အလုပ်လုပ်သောခါးပတ်၏မျက်နှာပြင်တွင် မြဲမြံစွာလိုက်နာနိုင်သော ပူးတွဲပါဖိုင်များကို ချက်ခြင်းဖယ်ထုတ်ပြီး ပုံစံများဖန်တီးရန် extruded ထုတ်ကုန်၏မျက်နှာပြင်တွင် ကပ်ထားသည်။extrusion ရပ်တန့်သွားသောအခါတွင်ပေါ်လာသောအလုပ်လုပ်ခါးပတ်၏အလျားလိုက်အစင်းကြောင်းများကိုကားပါကင်အမှတ်အသားဟုခေါ်သည်။extrusion လုပ်ငန်းစဉ်အတွင်း ပေါ်လာသော အစင်းကြောင်းများကို instant impressions သို့မဟုတ် bite marks ဟုခေါ်ပြီး ၎င်းတို့ကို extrusion အတွင်း အသံထွက်ပါမည်။
မှတ်တိုင်များ၊ ချက်ခြင်းအမှတ်အသားများနှင့် ကိုက်ခြင်းများ၏ အဓိကအကြောင်းရင်းများ
1. မညီမညာသောအပူအပူချိန် သို့မဟုတ် extrusion အမြန်နှုန်းနှင့်ဖိအားတွင်ရုတ်တရက်ပြောင်းလဲမှု;
2. မှို၏ အဓိက အစိတ်အပိုင်းများသည် ဒီဇိုင်းနှင့် ထုတ်လုပ်မှု ညံ့ဖျင်းခြင်း သို့မဟုတ် တပ်ဆင်မှု မညီမညာဖြစ်ပြီး ကွာဟမှုများ ရှိနေပါသည်။
3. extrusion direction နှင့် perpendicular ပြင်ပ force တစ်ခု ရှိပါသည်။
4. extruder သည် ချောမွေ့စွာ မလည်ပတ်နိုင်ဘဲ တွားသွားသည့် ဖြစ်စဉ်တစ်ခု ရှိပါသည်။
ကာကွယ်နည်း
1. မြင့်မားသောအပူချိန်၊ နှေးကွေးသောအမြန်နှုန်းနှင့်ယူနီဖောင်း extrusion၊ extrusion force တည်ငြိမ်နေဆဲ;
2. ထုတ်ကုန်အပေါ် တည့်မတ်ခြင်းမှ ဒေါင်လိုက် extrusion လမ်းကြောင်းရှိ ပြင်ပအားအား တားဆီးပါ။
3. ကိရိယာများနှင့် မှိုများ၏ ကျိုးကြောင်းဆီလျော်သော ဒီဇိုင်း၊ မှိုပစ္စည်းများ၏ မှန်ကန်သောရွေးချယ်မှု၊ အရွယ်အစားကိုက်ညီမှု၊ ခိုင်ခံ့မှုနှင့် မာကျောမှု။
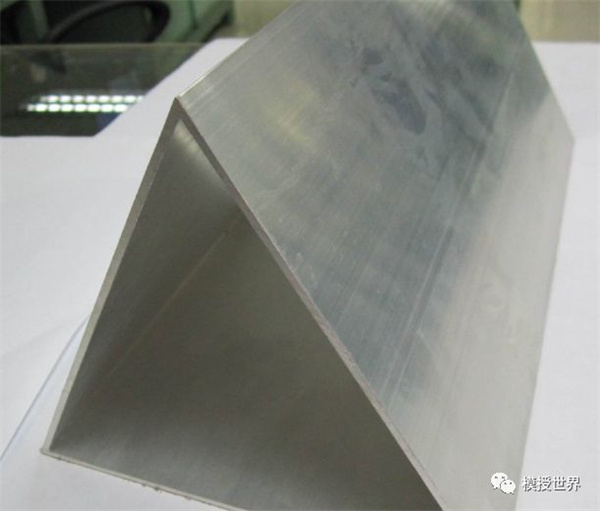
XXVIIIအတွင်းမျက်နှာပြင်တွင်ခြစ်ရာများ
extrusion လုပ်ငန်းစဉ်အတွင်း extruded ထုတ်ကုန်၏အတွင်းမျက်နှာပြင်ရှိခြစ်ရာများကိုအတွင်းမျက်နှာပြင်ခြစ်ဟုခေါ်သည်။
အတွင်းမျက်နှာပြင်ပွန်းပဲ့ခြင်း၏အဓိကအကြောင်းရင်း
1. extrusion needle ကို သတ္တုဖြင့် ကပ်ထားသည်။
2. extrusion needle ၏ အပူချိန် နိမ့်ပါသည်။
3. extrusion needle ၏ မျက်နှာပြင် အရည်အသွေးသည် ညံ့ဖျင်းပြီး အဖုအထစ်များ ရှိပါသည်။
4. extrusion temperature နှင့် speed ကို ကောင်းမွန်စွာ မထိန်းချုပ်နိုင်ပါ။
5. extrusion ချောဆီ၏မသင့်လျော်သောအချိုးအစား;
ကာကွယ်နည်း
1. extrusion ဆလင်ဒါ နှင့် extrusion needle ၏ အပူချိန်ကို တိုးမြင့်စေပြီး extrusion temperature နှင့် extrusion speed ကို ထိန်းချုပ်ပါ။
2. ချောဆီစစ်ထုတ်မှုကို အားကောင်းစေခြင်း၊ စွန့်ပစ်ဆီများကို မကြာခဏ စစ်ဆေးခြင်း သို့မဟုတ် အစားထိုးခြင်းနှင့် ဆီအညီအမျှ သင့်လျော်စွာ လိမ်းပေးပါ။
3. သိုးမွှေးမျက်နှာပြင်ကို သန့်ရှင်းအောင်ထားပါ။
4. အရည်အချင်းမပြည့်မီသော မှိုများနှင့် ထုတ်ပိုးထားသော ဆေးထိုးအပ်များကို အချိန်မီ အစားထိုးပြီး ထုတ်ယူသည့်မှိုများ၏ မျက်နှာပြင်ကို သန့်ရှင်းချောမွေ့အောင်ထားပါ။
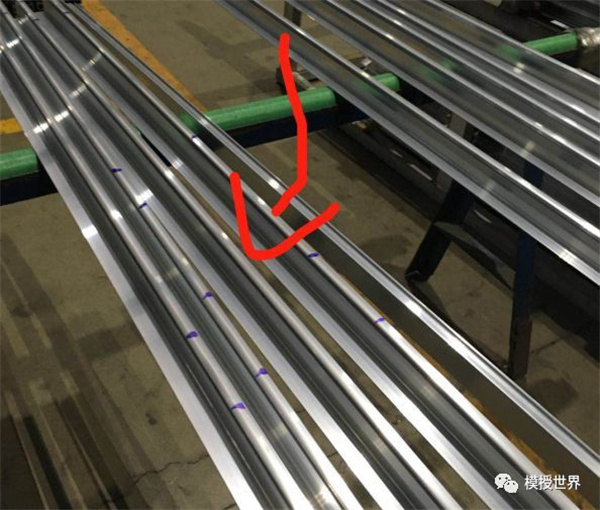
XXXအခြားအချက်များ
တစ်နည်းအားဖြင့် ကျယ်ကျယ်ပြန့်ပြန့် ကုသမှုခံယူပြီးနောက် အထက်ဖော်ပြပါ အလူမီနီယံ အလွိုင်းထုတ်ခြင်း ထုတ်ကုန်များ၏ ချို့ယွင်းချက် အမျိုးပေါင်း 30 ကို ထိရောက်စွာ ဖယ်ရှားနိုင်သည်၊ အရည်အသွေးမြင့်၊ အထွက်နှုန်းကောင်း၊ တာရှည်ခံကာ လှပသော ထုတ်ကုန်မျက်နှာပြင်ကို ဖန်တီးကာ အမှတ်တံဆိပ်တစ်ခု ဖန်တီးကာ တက်ကြွမှုနှင့် ကြွယ်ဝမှုကို ဆောင်ကြဉ်းပေးနိုင်ပါသည်။ လုပ်ငန်းနှင့် နည်းပညာပိုင်းနှင့် စီးပွားရေးဆိုင်ရာ အကျိုးကျေးဇူးများ သိသိသာသာရရှိခြင်း။
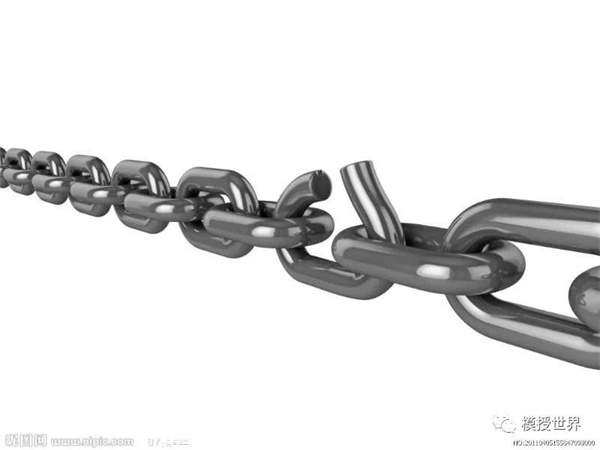
XXXအခြားအချက်များ
တစ်နည်းအားဖြင့် ကျယ်ကျယ်ပြန့်ပြန့် ကုသမှုခံယူပြီးနောက် အထက်ဖော်ပြပါ အလူမီနီယံ အလွိုင်းထုတ်ခြင်း ထုတ်ကုန်များ၏ ချို့ယွင်းချက် အမျိုးပေါင်း 30 ကို ထိရောက်စွာ ဖယ်ရှားနိုင်သည်၊ အရည်အသွေးမြင့်၊ အထွက်နှုန်းကောင်း၊ တာရှည်ခံကာ လှပသော ထုတ်ကုန်မျက်နှာပြင်ကို ဖန်တီးကာ အမှတ်တံဆိပ်တစ်ခု ဖန်တီးကာ တက်ကြွမှုနှင့် ကြွယ်ဝမှုကို ဆောင်ကြဉ်းပေးနိုင်ပါသည်။ လုပ်ငန်းနှင့် နည်းပညာပိုင်းနှင့် စီးပွားရေးဆိုင်ရာ အကျိုးကျေးဇူးများ သိသိသာသာရရှိခြင်း။
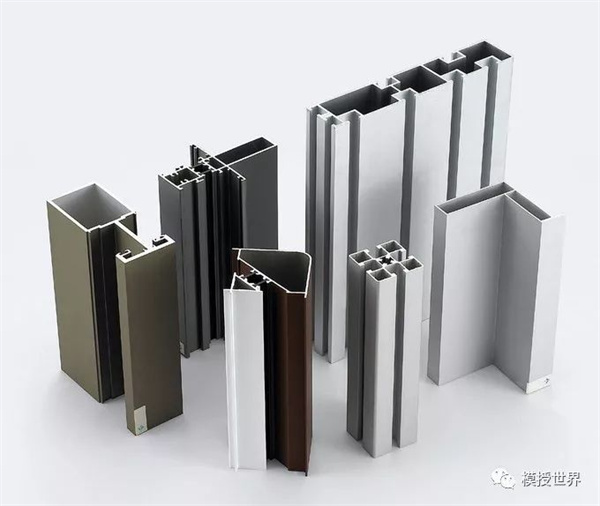
စာတိုက်အချိန်- သြဂုတ်-၁၄-၂၀၂၂